Lean Production: Toyota massimizza i profitti e azzera gli sprechi
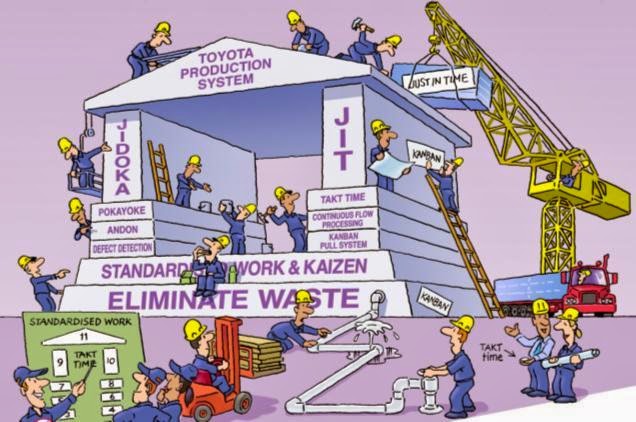
Massimi profitti e zero sprechi: due realtà che possono coesistere?
Lean Manufacturing and production
Con il termine Lean Manufacturing o Lean Production si identificano tutti quei metodi di organizzazione e produzione aziendale che combattono la lotta agli sprechi e puntano alla massimizzazione del profitto. Questo tipo di produzione ‘snella’ (traduzione italiana di ‘lean’) si pone diametralmente al contrario rispetto il concetto di Fordismo (produzione di massa).
Massimi profitti e zero sprechi: nasce tutto con Toyota
Tutto nasce in Giappone negli anni ‘50 dalle idee di Sakichi Toyoda, Kiichiro Toyoda, Taiichi Ohno, fondatori e dirigenti della rinomata ‘Toyota’. Il mercato automotive di quegli anni era dominato dagli USA che basavano il loro lavoro sulla produzione di massa. Nel 1950 la Toyota sviluppò un nuovo sistema di produzione (Toyota Production System) che fondava tutto su una semplice quanto potente idea: fare di più con meno. Nel profondo di questa idea c’era la volontà di utilizzare il minor numero di risorse possibili e reperibili nel modo più produttivo possibile. Questo modo di fare nasce da analisi sul mercato automobilistico del 1900. Negli USA la produzione di massa garantiva prezzi contenuti e numeri elevati (elementi che garantivano una grande richiesta nel mercato). Il problema risiedeva nelle lavorazioni e nel processo di produzione: erano molti i casi di guasti e difetti. Le aziende automobilistiche avevano grandi spese di manutenzione sia nei processi che nei prodotti finiti. Da queste analisi nasce il sistema Toyota: evitare tutti gli sprechi, non avere difetti.
I principi della Lean Production
La prima parola chiave della Lean Production è ‘il valore’. Del tempo totale impiegato per la produzione di un prodotto (ricerca risorse, tempi di consegna, di lavorazione, di trasporto …) quelle che sono ‘a valore’ per il cliente sono solo una parte minima. La produzione deve quindi orientarsi ridurre tutto quello che è considerato uno spreco, che nella terminologia della Lean viene indicato con MUDA. I Muda da eliminare (o comunque ridurre al minimo) sono 7:
- Difetti nei prodotti (e quindi nella tecnica)
- Sovrapproduzione non necessaria di prodotti (non deve esserci prodotto invenduto)
- Magazzini pieni di materie prime o semi lavorati in attesa di ulteriori processi
- Lavorazioni non necessarie, che non hanno cioè valore per il cliente
- Spostamenti non necessari di persone (organizzazione degli spazi e del personale)
- Trasporti non necessari di beni
- Attese del personale (tra una lavorazione e l’altra)
La catena del valore
Il processo di ottimizzazione non può limitarsi all’interno della azienda e/o ai soli processi interni. Il prodotto nasce quando viene ‘richiesto’ e termina il suo processo solo quando è consegnato. A monte e a valle del processo di produzione vi sono moltissimi altri momenti che devono essere analizzati ed ottimizzati (eliminandone i Muda). Bisogna allora costruire una catena del valore di tutto il sistema di produzione: fornitori, trasposti, azienda, distributori, mercato. L’intera catena deve puntare alla massimizzazione di tutto il sistema.
Il flusso come terzo principio della Lean Production
Il processo di produzione deve ‘fluire’ in modo costante, continuo, senza attese, pause, soste, cambi. Questo è possibile solo se non vi sono organizzazioni segmentate o contrapposte, complementari. Bisogna organizzare il processo produttivo tramite fasi interdipendenti che convergono tutte al medesimo risultato. Per questo motivo nella Lean Production decade l’idea di ‘reparto’ a favore della produzione di linea riducendo i tempi morti o di attesa tipici delle produzioni a ‘batch’ (gruppi di semilavorati che si spostano da un reparto ad un altro dopo aver raggiunto un certo numero).
Tiro della domanda (sistema PULL) e perfezionamento
La produzione Lean gestisce la domanda in maniera Pull. Il cliente richiede il prodotto prima, non esiste più la produzione preventiva con l’uso dei magazzini e non esiste un punto di arrivo: bisogna sempre migliorare il processo, indipendentemente dai metodi della concorrenza.
Organizzazione e controllo nella Lean Production
Al vertice della Lean production abbiamo il cliente, con le sue aspettative e con il valore che è disposto a dare per il prodotto che l’azienda gli deve fornire. Le idee principali (Zero sprechi da un lato e il valore dall’altro) si attuano con diverse strategie. Il sistema è di tipo Pull come già descritto: si utilizza la tecnica KANBAN.
Il sistema deve prevedere un Takt Time (TT) che è il ritmo della produzione calcolato sul ritmo della domanda. Data la domanda è la scadenza trovo un Takt (ad es. 100 pezzi/ora) che deve essere uguale in tutti i processi che portano al prodotto finito. Il sistema Jidoka è la progettazione di macchine intelligenti, che si arrestano quando vi sono difetti. Tutto l’impianto deve essere a prova di errore. La probabilità di avere difetti deve essere praticamente nulla. Questo si attua con il lavoro standardizzato: il processo è interamente stabilito e controllato in tutte le sue attività, non ci sono variazioni e non esistono aggiustamenti in itinere. Il metodo Kaizen è a programmazione di progetti mirati nel breve periodo che coinvolgono tutto il personale con lo scopo di un miglioramento continuo della qualità e produttività. Per questo scopo è nata la ‘Visual Management’ che consiste nel creare schede, lavagne, post-it in ogni linea di produzione con l’avanzamento del processo, lo stato attuale del lavoro svolto e i tasks o jobs svolti da ogni operaio/dipendente.
Articolo a cura di Simone Americi